As part of the mobile minigrid project in Kenya, we have been working with Chemolex and Quantum Conversions in Nairobi, on designing a trailer with 10kW of quickly deployable solar power. So what does that look like?
Well 10kW of solar power is BIG! Each 430W panel is over 2mx1m (almost the size of the roof of the trailer), and we’ll need 20 of them. We’ve decided to pay the extra cost for lightweight flexible panels, enabling easier transportation (each panel is only 2mm thick, weighing just over 7kg), but that doesn’t change how much area they’ll need when set up to catch the sun’s rays.
We started by brainstorming different concepts for unfolding solar panels, taking inspiration from solar satellites, unfolding ladders, existing containers with deployable solar, and cars/boats with solar power. From these 15 concepts, we narrowed down those that were most promising for further development.
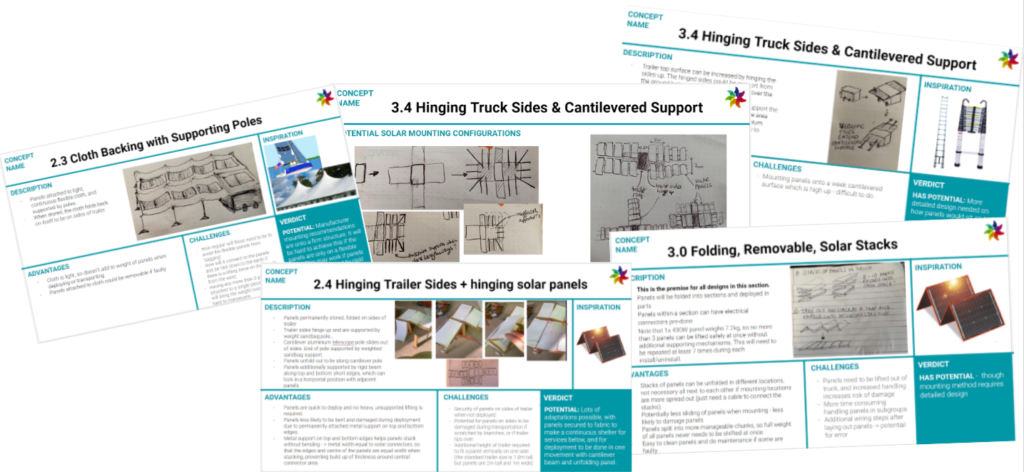
Next up was a bit of hands-on testing – using cardboard for prototyping! This really illustrated the scale of the challenge: how big the panels would be in relation to the trailer, how easy it would be for an operator to open up the panels, and mechanical challenges when it comes to different sliding mechanisms.
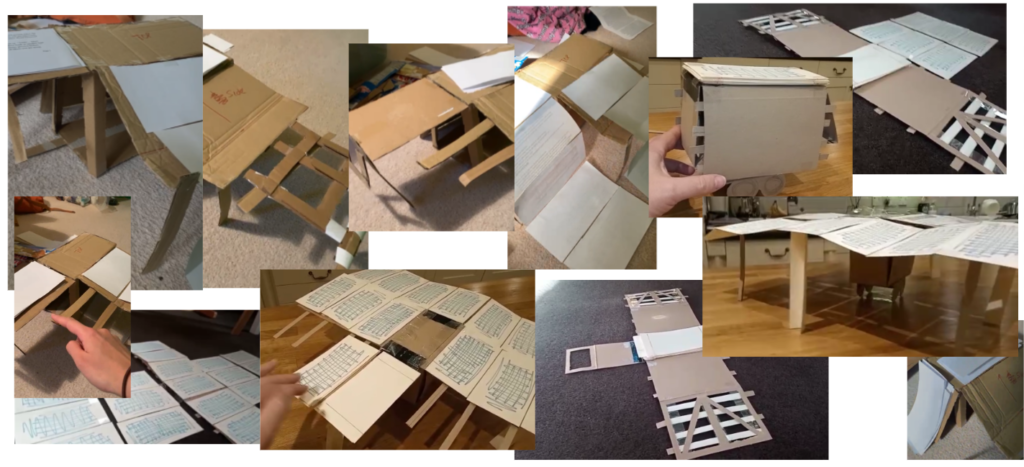
Once the ideas were a bit more fleshed out, the most promising design was drawn up in CAD.
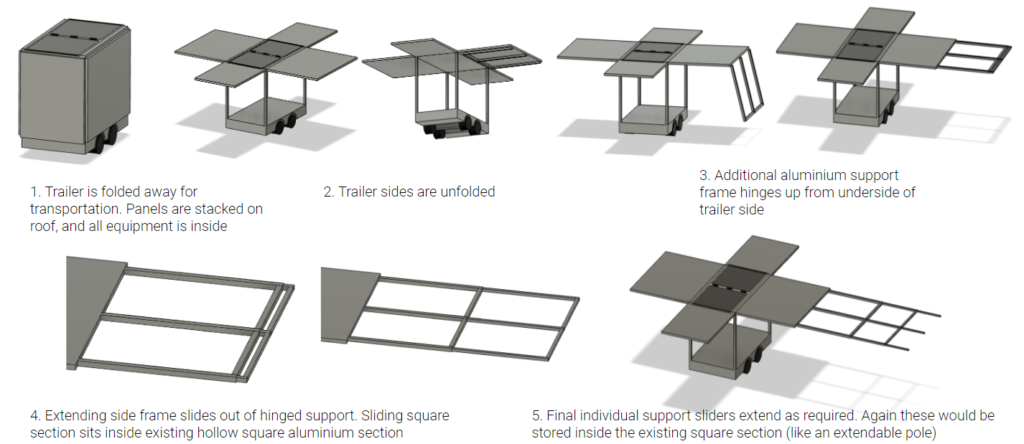
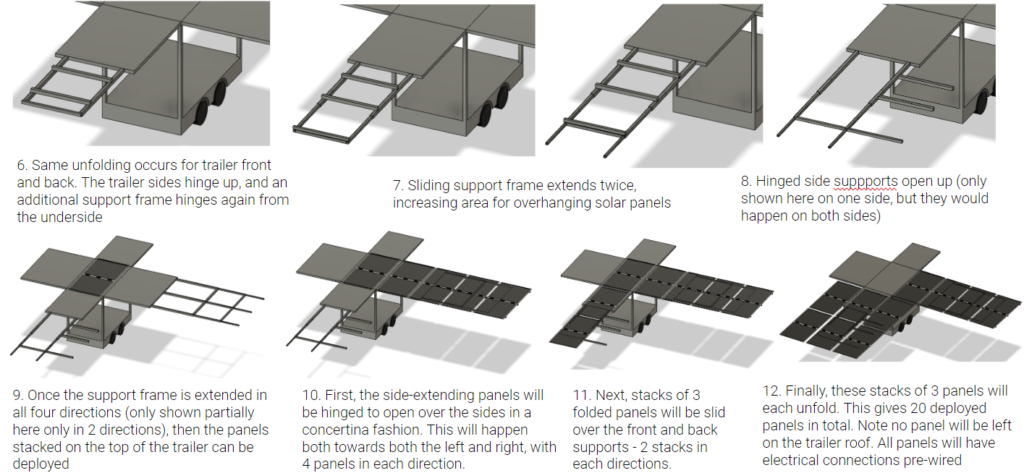
The team in the workshop tested some of their own ideas, highlighting an even better method for unfolding solar panels from the side of the trailer, rather than the roof! We really liked this idea, and decided to develop it going forwards. We will have four panels unfolding from each of the trailer sides, and an additional 6 sliding out the front and back of the trailer, to unfold alongside.
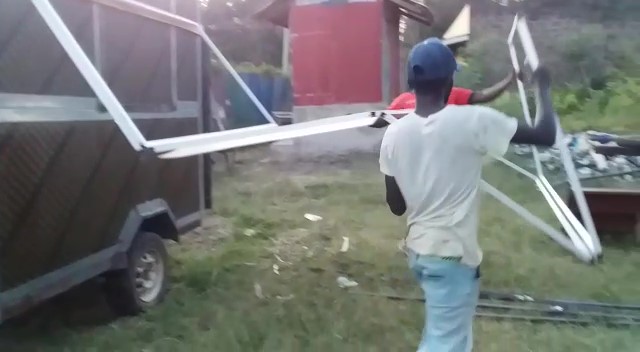
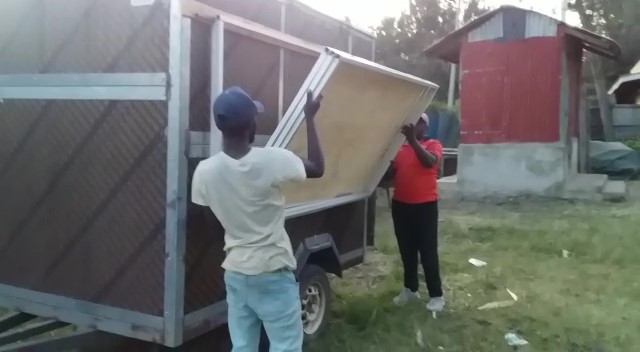
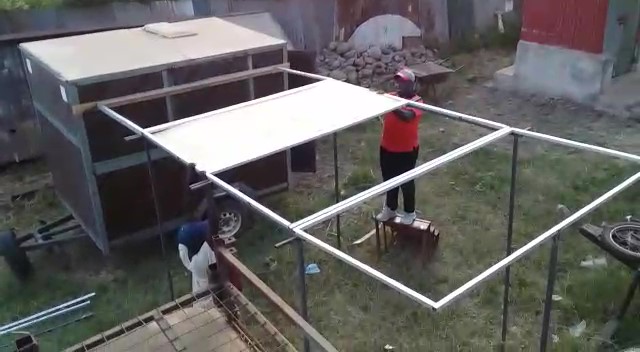
And then it was onto more full-scale prototyping. As the solar panels haven’t yet arrived from China, we decided to test with 3mm plywood. We made mock-ups of the panels (connectors included as they add an extra 2cm to the thickness of the panel, which would otherwise be only 2mm!) and tested a new support frame idea with thin aluminium strips – minimising metal and weight. We had a much smaller 0.5x1m flexible solar panel to compare with, and although we learnt a lot from the prototyping, it is clear we will need to test again once we have the solar panels as they will be much less rigid!
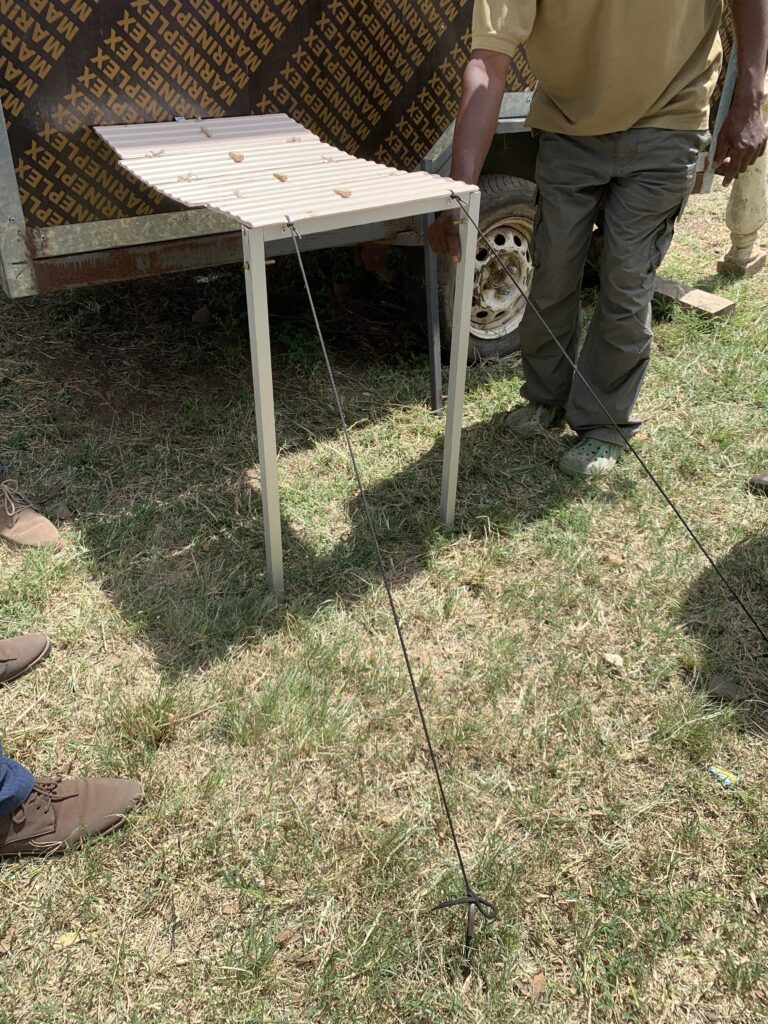
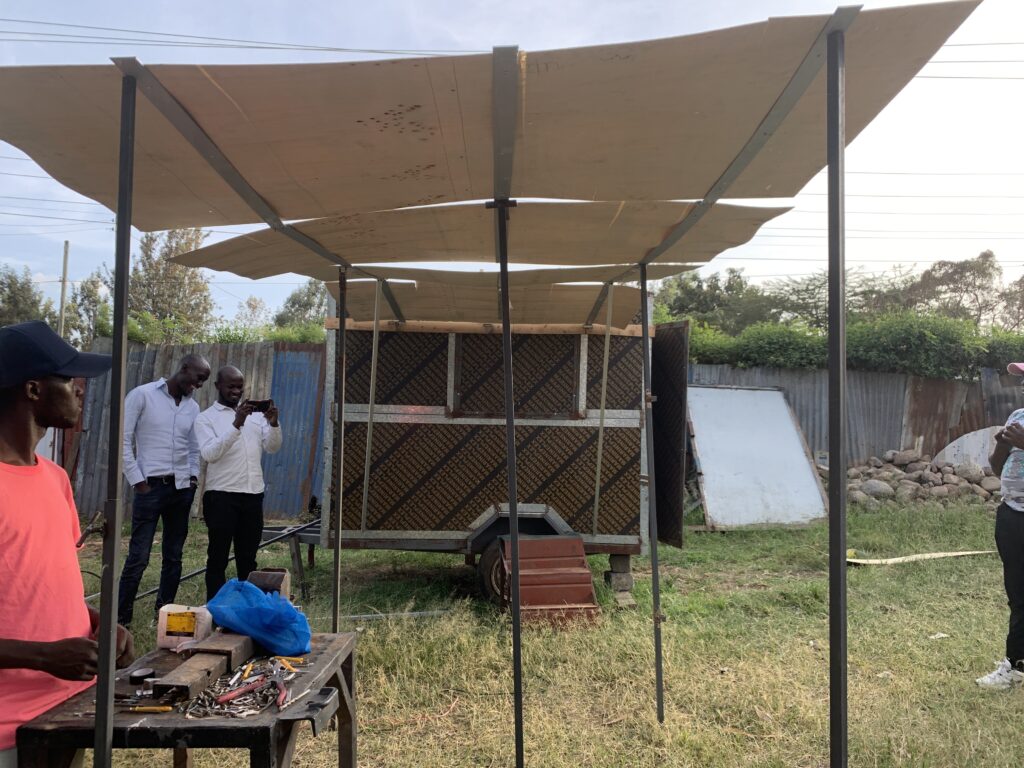
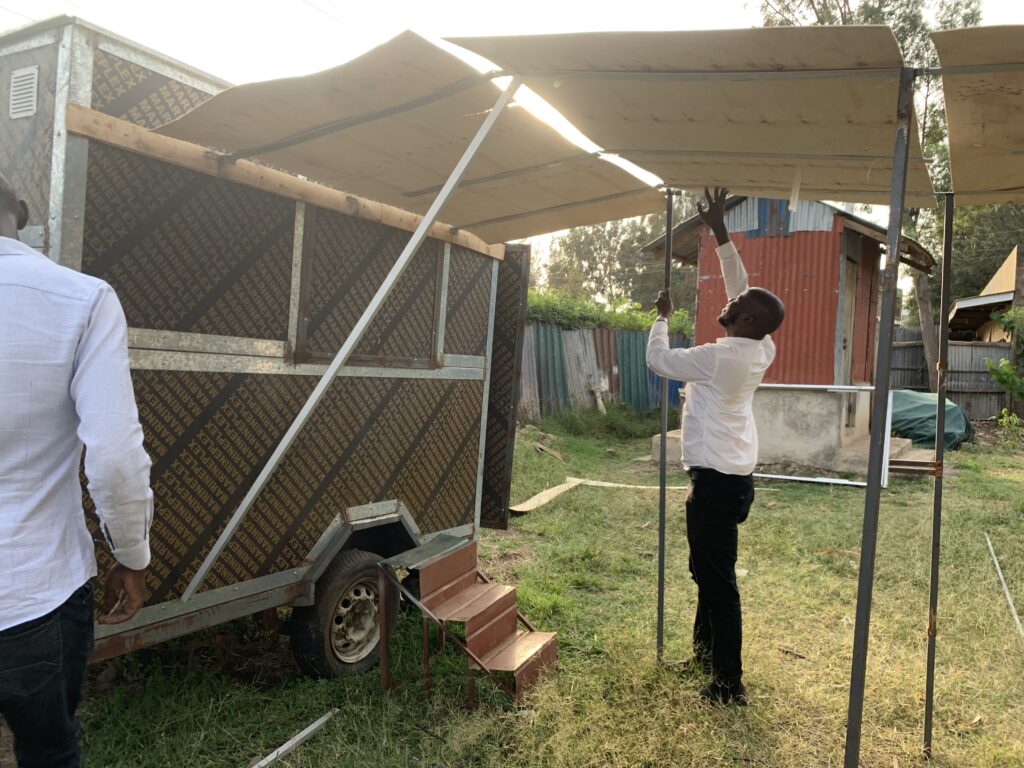
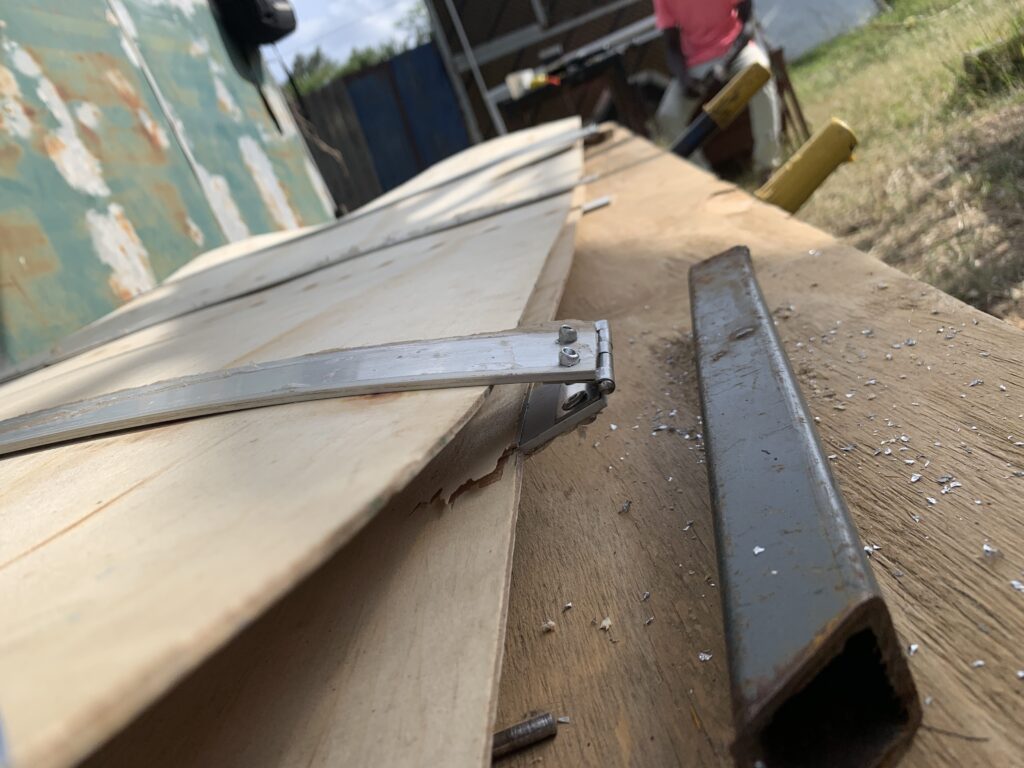
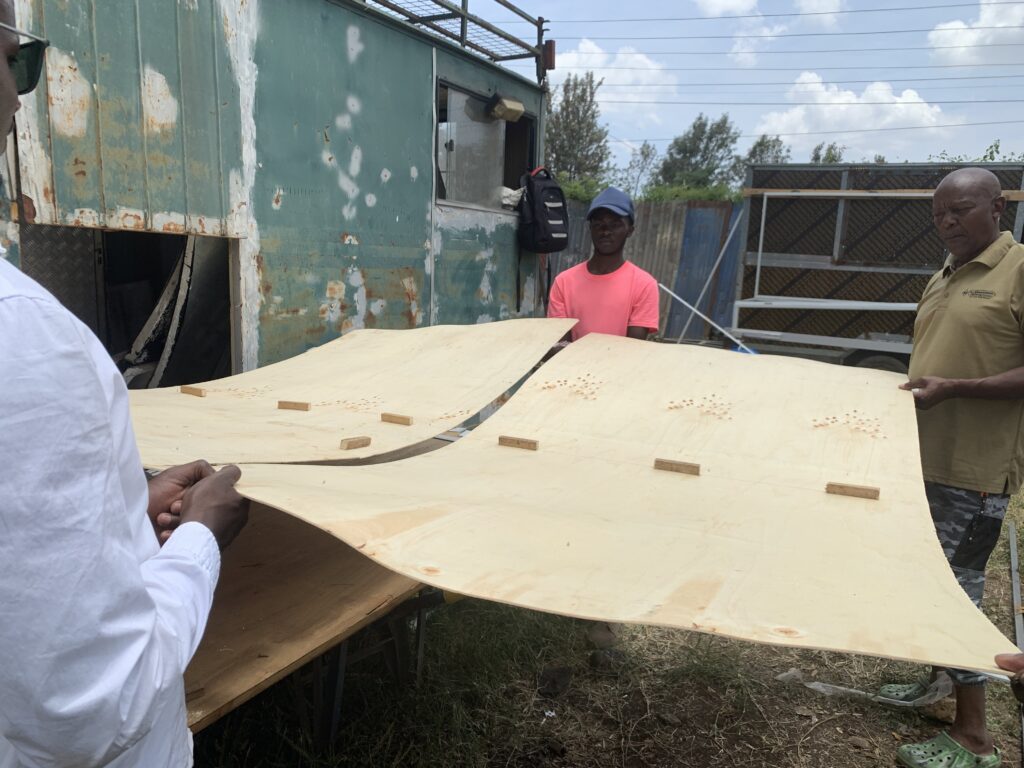
Having tested the ideas in the workshop, we are feeling positive about the design going forwards and excited to see it develop as parts arrive and things come together!